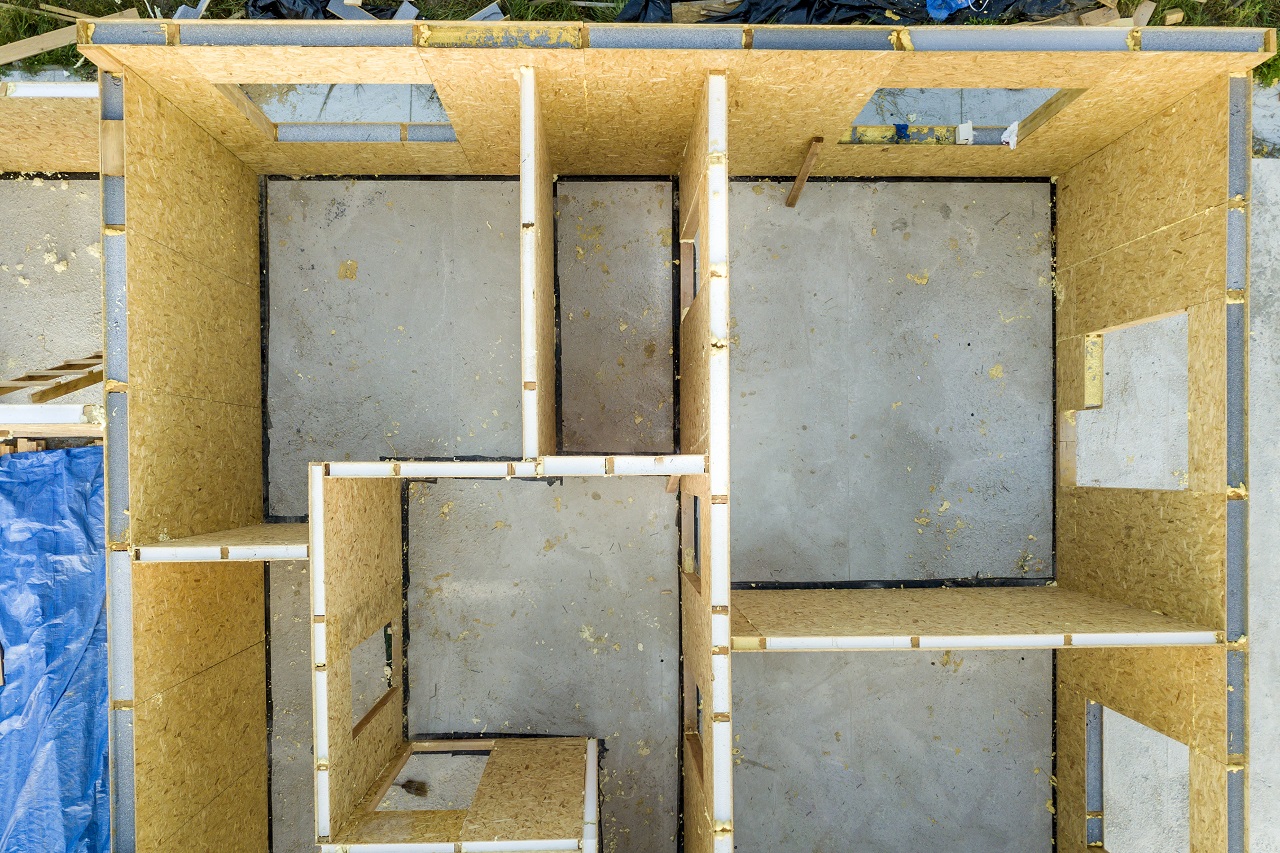
Construction of new and modern modular house. Walls made from composite wooden sip panels with styrofoam insulation inside. Building new frame of energy efficient home concept.
Once a somewhat niche market that only appealed to certain kinds of buyers and builders, the market for pre-fabricated homes has seen an increase in popularity during the pandemic. The relative ease of construction, combined with lower costs and greater flexibility, has opened up a new demand for pre-fabricated spaces as homeowners search for solace in the midst of a prolonged era of social distancing.
According to Steve Glenn, CEO of the Santa Monica-based company Plant Prefab, the firm has seen a 50% increase in contracts over last year. This could be partially due to an uptick in buyers looking for more space outside of major cities, but there are several other benefits to pre-fabricated homes as well.
Unlike onsite construction, which is often costly and time-consuming, pre-fabricated construction has added certainty when it comes to the cost and time required to complete construction. Building the components in a factory means construction is not subject to the same external challenges of onsite construction, and factory work also allows workers to social distance more safely, as each worker can remain at their station.
Additionally, pre-fabricated structures can be modified more easily ahead of time, allowing buyers greater control over which features they’d like to see in the final product. Some of the most common requests of late, according to New York’s Resolution: 4 Architecture, include COVID-conscious design features like flexible living spaces, work-from-home spaces and home gyms. Other popular additions include mud rooms and even accessory dwelling units (ADUs) for those who want to add a separate office space or guest space where they can work uninterrupted.
But pre-fabricated homes are not just for the suburbs or plots of land in the countryside. With land in major cities becoming more affordable due to the changing demands of COVID-19, some pre-fabrication firms have also been developing modular and multi-family residences for use in denser urban areas. Pre-fabrication firm FullStack Modular has even developed modular medical units that can be used for the isolation and testing of COVID-19 patients.
With demand for pre-fabricated designs expanding to include modular restaurants and even socially-distant cabins for use in the hospitality industry, the possibilities for pre-fabricated structures are endless.
This article was originally posted on Architectural Digest by Sam Lubell and GettheWReport.com